The use of contractors is commonplace in many industries to carry out specialised work or help manage fluctuating workloads. However, with contractors comes risks – if contractor safety is not managed properly, it can lead to incidents, injuries and even fatalities. This negatively impacts a company’s reputation and bottom line through fines, lawsuits and project delays. Implementing a robust contractor safety program is therefore critical.
Pre-qualifying Contractors
The first step is vetting and pre-qualifying prospective contractors on their safety records. Review their procedures, training, and past safety performance through metrics like lost time incident rates. Check that they have adequate insurance coverage for the intended work. Guidance from organisations like Build UK provides best practices for pre-qualification requirements across various industries. Setting clear expectations and standards at the outset ensures only capable, safety-focused contractors are engaged.
Contractual Safety Requirements
All contracts with contractors should include explicit safety expectations, such as compliance with your company’s safety policies and all applicable legislation like the Health and Safety at Work Act [1]. Contracts should also grant you the right to audit contractor safety measures. Clearly defining these requirements codifies accountability. The Safety Schemes in Procurement (SSIP) forum publishes model contract conditions for member industry schemes that provide helpful guidance.
Site Induction and Training
Don’t assume contractors arrive ready to work safely on your site. All contractors should undertake a site induction highlighting hazards, rules and emergency procedures. Ensure they receive any additional training needed for the intended work like working at heights, confined space entry or electrical safety. Maintaining training records also provides legal duty of care evidence.
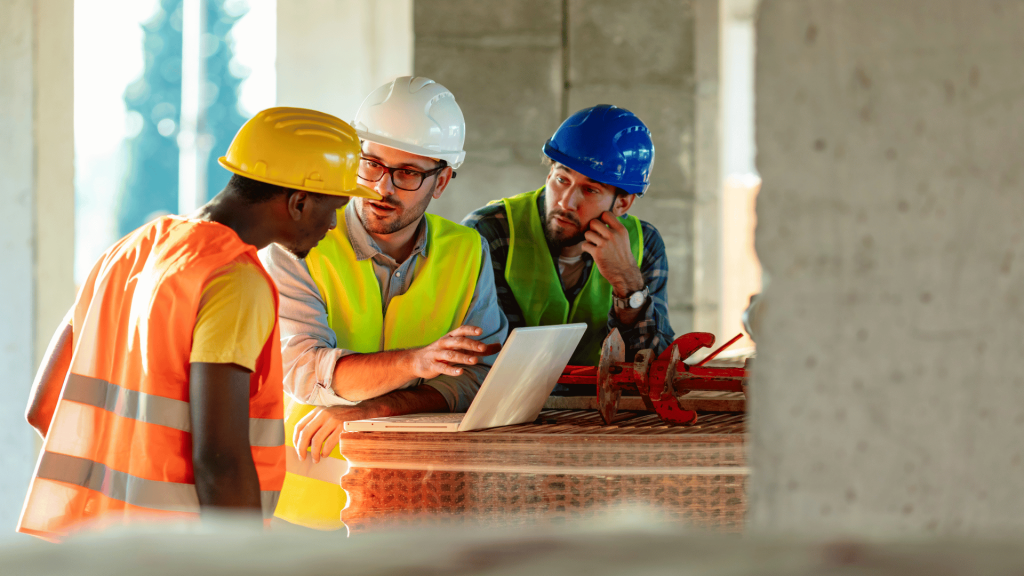
Hazard Identification and Risk Assessments
Contractors have prime responsibility for identifying hazards and controlling risks from their activities that could affect your workers or theirs. Review the adequacy of their risk assessments and method statements. High-risk activities like hot works, power isolations or work at height require permits to ensure proper precautions are in place.
Ongoing Monitoring
It takes more than just initial reviews to manage contractor safety risks during work. Supervisors should regularly check in on contractor activities, supplemented by senior management spot checks on critical safety compliance. Particularly scrutinise high-risk activities. A key focus area should be housekeeping – a leading indicator of overall safety diligence.
Incident Reporting and Investigation
All contractor incidents, from minor first aids to major incidents require reporting and investigation per company procedures. Clearly communicate expectations and reporting methods during induction. Incident investigations identify root causes and learnings that can improve safety for all on-site. Sharing lessons learned across contractors prevents repeated mistakes.
Review and Evaluation
There should be regular, formal contractor safety reviews conducted jointly between contractors and company representatives. Evaluate measures like lead and lag metrics, audit performance and risk assessment adequacy. Compare contractor performance metrics like incident rates. Reviews identify areas for praise and improvement. Share constructive feedback so contractors continuously improve their safety practices.
Managing contractor safety requires clear standards reinforced continually through induction, training, monitoring, review and open communication. Duty of care extends to ensuring the safety of contracted personnel onsite. A consistent focus on contractor safety improves outcomes for all personnel on site and enhances public perception of your company’s safety commitment.
Promoting a Positive Safety Culture
Simply enforcing rules is not enough to drive contractor safety excellence – there must be a commitment from both contractors and your company to foster a positive safety culture. This starts from the top with senior leaders actively demonstrating safety leadership rather than just preaching policies. Contractors should be recognised for proactive safety initiatives, reporting near misses, conducting quality risk assessments and helping co-workers work safely. Likewise, your company’s staff must exemplify safety leadership when working alongside contractors.
There should be open communication channels for contractor personnel to voice safety concerns without fear of retribution. Consider regular town hall meetings for contractors and employees to discuss hazards, controls and safety improvement suggestions.
Small positive reinforcements are also powerful – something as simple as “well done” and public praise when observing contractors working safely. When people feel their contributions are valued, it promotes engagement and motivation to look out for themselves and others.
Senior management commitment, open collaboration, recognition and frequent positive reinforcement of safe behaviours drive contractor buy-in to your company’s safety vision and create a collective culture of care. This ultimately leads to higher safety compliance and fewer incidents. A recent EU-OSHA report provides multiple case studies where organisations applied these cultural principles to improve contractor safety in practice.
Conclusion
Managing contractor safety entails effort from planning to execution to ensure control of risks from contracted work. Contractor management requires rigorous standards and continuous oversight, from initial screening to incident review. However, implementing a comprehensive safety management process drives benefits for both contractors and your company. Contractors work more efficiently in an organised environment with clear guidelines. For your company, properly managed contractor safety reduces potential hazards to your staff and assets. It also highly minimises the chances of serious incidents occurring. This prevents damage to both your company’s finances and reputation in the long run. Ultimately, the commitment to cultivating a positive safety culture with contracted partners fosters collaboration and accountability from all parties to achieve an accident-free workplace.
What aspects outlined here resonate with your experience managing contractor safety? What key challenges have you faced or what practical solutions have worked for your company? Please share your perspectives or recommendations in the comments. Getting views from a range of industries helps spark ideas we can all use to enhance safety outcomes.